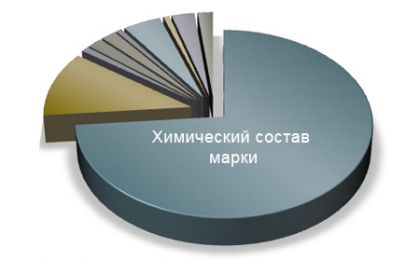
Почему металл бывает магнитным, твердым, мягким и имеет сопротивление к коррозии и абразии?
Понимание типов металла, используемого в производстве насосов
Так же как и любая другая аустенитная нержавеющая сталь, сталь сорта 316 является очень мягкой. Так почему же эта сталь предлагает мощную защиту от кавитации? Если она мягкая, будут ли взрывающиеся пузырьки разъедать материал?
Нержавеющая сталь обеспечивает отличное сопротивление кавитации благодаря своим свойствам деформационного упрочнения. На поверхности необработанной стальной ленты может возникнуть вмятина. Однако после нескольких ударов по ленте молотком возникновение вмятин осложняется – поверхность упрочнении вследствие деформации. Как ни странно, мягкость нержавеющей стали является причиной сложности ее обработки – она упрочняется, когда режущий инструмент проходит через нее, и образуется стружка и зазубренная кромка вместо ровного и гладкого надреза.
Тот же процесс происходит, когда кавитационные пузырьки атакуют поверхность нержавеющей стали. Поверхность упрочняется, и возникает сопротивление дальнейшей кавитации. Из-за деформационного упрочнения нержавеющая сталь сорта 316 (CF8M) сопротивляется кавитации в 10-15 раз лучше, чем чугун. Дальнейшие металлургические доработки могут повысить сопротивление нержавеющей стали кавитации. К примеру, литая нержавеющая сталь (CA6NM) имеет в три раза большее сопротивление кавитации, чем сталь сорта 316.
Одним из самых популярных материалов среди аустенитных сталей является нержавеющая сталь 316. Она содержит 16-18% хрома и 10-14% никеля, которые являются основными компонентами ее сплава. Также в ней присутствует 2-3% молибдена, а количество углерода ограничено 0,08%. Если количество углерода уменьшить до 0,03%, то такая сталь называется 316L.
Аустенитные нержавеющие стали (которые иногда называются сталями сорта 18-8 (18% хрома, 8% никеля) обладают превосходным сопротивлением коррозии. Такую сталь невозможно закалить, кроме холодной закалки, что приводит к сопротивлению кавитации.
Другой важной группой нержавеющих сталей являются мартенситная и ферритная сталь. Серия 400 – это мартенситная нержавеющая сталь, и она является магнитной. Серия 300 – это аустенитная сталь, и она является немагнитной. Магнитные свойства нержавеющей стали зависят от ее состава (компоненты сплава) и способа ее производства (термическая обработка).
Основным компонентом сплава нержавеющей стали 431 является хром – ровно 16%, который усиливает сопротивление коррозии, и по этому показателю сталь 431 значительно превышает простую углеродистую сталью. Также хром делает сталь упрочняемой, и именно поэтому мартенситные сплавы отлично подходят для валов насосов. Мартенситные сплавы являются прочными.
Во время первой отливки в цеху нержавеющая сталь имеет аустенитную структуру при высокой температуре и охлаждается после заливки. Во время охлаждения аустенит начинает преобразовываться в мартенсит – примерно при температуре 770 C (1418 F). Некоторые компоненты сплава, включая хром и никель, могут отложить или предотвратить это преобразование. Металлурги используют схему Шеффлера, на которой изображены эквиваленты хрома и никеля, которые требуются для поддержания мартенситного или аустенитного состояния сплава (см. Рисунок 1).
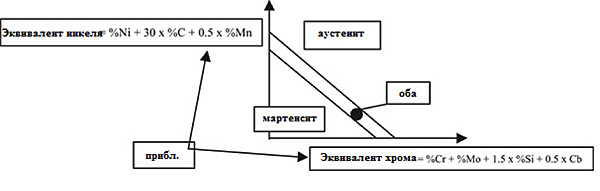
Рисунок 1. Схема Шеффлера
Добавление никеля помогает нержавеющей стали 316 оставаться в зоне аустенита. Нержавеющая сталь 431 содержит только хром, поэтому она преобразуется в мартенситную структуру.
Инспекторы оборудования обычно применяют быстрый тест, чтобы убедиться, что деталь сделана из нержавеющей стали 361. Они используют магнит и пытаются притянуть его к детали. Если магнит притягивается, они понимают, что что-то не так, так как нержавеющая сталь 316 является аустенитной и немагнитной. Однако иногда чувствуется слабое притяжение магнита к детали из такой стали. Это может говорить о наличии небольшого количества остаточного мартенсита в структуре.
Существует множество выражений для эквивалентных сварных изделий хрома и никеля. Схемы Шеффлера, Шофера и Делонга – это лишь некоторые примеры. Схемы Делонга включают влияние азота в выражениях эквивалента никеля.
К примеру, схема Шеффлера, указывающая количество феррита и аустенита, присутствующего в сварной детали, дает следующее выражение:
Эквивалент хрома =
%Cr + %Mo + 1.5 x %Si + 0.5 x %Nb (или Cb)
Примечание: ниобий (Nb) и колумбий (Cb) – это один и тот же элемент.
Эквивалент никеля = %Ni + 30 x %Cr + 0.5 x %Mn
Схема Шофера для оценки среднего содержания феррита в аустенитных железо-хром-никелевых нержавеющих отливках указана в стандарте Американского общества специалистов по испытаниям и материалам (ASTM) A800 вместе со схемой для отношения эквивалента хрома (Creq)/эквивалента никеля (Nieq).
Содержание феррита в отливках оценивается на основе соотношения составов эквивалента хрома и никеля. На основе схемы Шофера уравнения представлены в немного другом виде:
Эквивалент хрома =
%Cr + 1.4 x %Mo + 1.5 x %Si + %Nb (or Cb) – 4.99
Эквивалент никеля =
%Ni + 30 x %C + 0.5 x %Mn + 26 x (%N – 0.02%) + 2.77
Содержание феррита в сварных деталях отливках устанавливается, главным образом, при помощи баланса между стабилизаторами феррита и аустенита или элементов, которые обычно образуют феррит или аустенит. Путем регулировки соотношения стабилизаторов феррита (хром, молибден, силикон и ниобий или колумбий) и стабилизаторов аустенита можно контролировать содержание феррита, которое также можно определить при помощи схемы Шофера в отношении содержания феррита в отливках, которая является адаптацией известной схемы Шеффлера, разработанной для прогнозирования микроструктуры нержавеющих сварных деталей.
Несмотря на то, что схемы Шеффлера, Шофера и Делонга обеспечивают достаточную точность, отливки следует оценивать при помощи схемы Делонга, хотя эта схема изначально создавалась для примесей сварного металла, и она включает влияние азота. Схема Делонга обеспечивает наибольшую точность прогнозов дельты феррита в аустенитных нержавеющих сталях.
Так как химический состав влияет на микроструктуру, в течение долгих лет было разработано множество эмпирических отношений и схем состава для прогноза микроструктуры. Во всех случаях эквиваленты хрома и никеля использовались для прогнозирования влияния различных добавок на отношение между образованием феррита и образованием аустенита.
Значительное расхождение касается отношений этих эквивалентов и формул. Как заметил Стивен Морроу, схема Шеффлера была разработана в 1940-х годах для прогнозирования микроструктур сварки. В 1988 году она была доработана Делонгом и исследовательским советом по сварочным работам (WRC), а затем тем же Советом еще раз в 1992 году.
Далее приводится обзор некоторых из этих отношений для эквивалентности никеля и хрома, однако имеются и многие другие измененные выражения:
• Шеффлер в 1949 году
• Эквивалент хрома = Cr + Mo + 1.5 Si + 0.5 Nb
• Эквивалент никеля = Ni + 0.5 Mn + 30 C
• Делонг в 1956 году
• Эквивалент хрома = Cr + Mo + 1.5 Si + 0.5 Nb
• Эквивалент никеля = Ni + 0.5 Mn + 30 C + 30 N
• Халл в 1973 году
• Эквивалент хрома = Cr + 1.21 Mo + 0.48 Si + 0.14 Nb + 2.27 V + 0.72 W + 2.20 Ti + 0.21 Ta + 2.48 Al
• Эквивалент никеля = Ni + (0.11 Mn – 0.0086 Mn квадратичный) + 24.5 C + 14.2 N + 0.41 Co + 0.44 Cu
• Хаммар и Свенсон 1979 году
• Эквивалент хрома = Cr + 1.37 Mo + 1.5 Si + 2 Nb + 3 Ti
• Эквивалент никеля = Ni + 0.31 Mn + 22 C + 14.2 N + Cu
• Зиверт 1992 году
• Эквивалент хрома = Cr + Mo + 0.7 Nb
• Эквивалент никеля = Ni + 35 C +20 N + 0.25 Cu
Поэтому в следующий раз, когда вы будете осматривать металлическую деталь, прикоснитесь к ней магнитом.
Надёжность с нами выбрали:
![]() |
![]() |
![]() |
![]() |
![]() |
![]() |
![]() |
![]() |
![]() |
![]() |
![]() |
![]() |
![]() |
![]() |
![]() |
![]() |
![]() |
![]() |
![]() |
![]() |
![]() |
![]() |
![]() |
![]() |